Effects of Mercury on an Aluminium Heat Exchanger in a Natural Gas Plant
Heat Exchange - Major Failure
At 2:43 am on the 1st of January 2004 an explosion and fire was caused by the failure of a cold box manifold. This destroyed one gas processing train and interrupted natural gas production for approx. 6 weeks. HRL Technology was commissioned to determine the root cause of this major failure.
The fire resulted from the failure of an inlet nozzle to a cold box which is part of the refrigeration process in the Liquid Recovery Plants (LRP). The findings from the HRL study, based on analysis of samples taken from the affected area, found that the failure of the inlet nozzle was due to liquid metal embrittlement (LME) of the aluminium cold box by elemental mercury. LME is a complex metal fracture mechanism that occurs without warning. Natural gas from subterranean reservoirs in Australia and South East Asia typically contains minute levels of elemental mercury.
The natural gas purchased by consumers consists almost entirely of methane, the simplest hydrocarbon. In gas reservoirs, however, methane is typically found in mixtures with heavier hydrocarbons - such as ethane, propane, butane and pentanes - as well as water vapour, hydrogen sulphide , carbon dioxide, nitrogen and other gases. Almost all of these substances are removed from the gas stream at processing plants located near production areas. The actual practice of processing natural gas to pipeline dry gas quality levels can be quite complex, but usually involves four main processes:
- Oil and Condensate Removal
- Water Removal
- Separation of Natural Gas Liquids (NGL)
- Sulphur and Carbon Dioxide Removal
Once NGLs have been removed from the natural gas stream, they are broken down into their base components and separated into different streams. The process used to accomplish this is called fractionation. Because the different NLGs have different boiling points fractionation can separate the constituents in stages by boiling off hydrocarbons one by one. The purpose of the LRP at the refinery is to recover the maximum amount of liquid hydrocarbon components from the gas feed utilising cryogenic fraction. This is accomplished by cryogenic distillation, separating ethane and heavier hydrocarbons from sales methane. Mercury is known to collect during this process.
The heat exchanger that failed is shown in Figure 1(a) and the failed nozzle is shown in Figure 1(b).
The failure investigation focussed on the failed nozzle that was relocated to the HRL laboratories in Mulgrave, Melbourne, Australia. A section from this nozzle is shown in Figure 2. All cracks and fracture surfaces were contaminated with elemental mercury and/or oxide whiskers consistent with mercury induced corrosion. Significant bulging of the manifold had occurred in the vicinity of the rupture, and there was extensive secondary cracking, particularly in areas showing
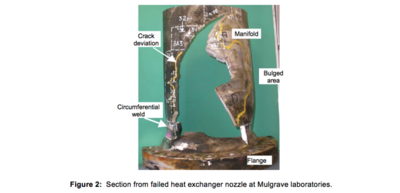
There was significant delamination cracking in the circumferential/longitudinal plane running from the longitudinal rupture for distances varying from 25-75 mm as shown in Figure 3(a) and significant fine branched cracking subsurface as shown in Figure 3(b) and Figure 4.
The brittle nature of the failure and observations of elemental Hg on the fracture surfaces, delamination of the aluminium nozzle material and branched intergranular cracking strongly suggested the failure had occurred through LME. Consequently an investigation was commenced into the likelihood of mercury induced LME in gas plants.
Types of Hg Attach in Aluminium Heat Exchangers
Mercury can occur in natural gas feed stock, sometimes in quantities sufficient to cause severe attack and failure of cryogenic aluminium heat exchangers and other gas conditioning and separation processes. The cooling equipment in a gas separation or dew point control process is typically an aluminium plate-fin heat exchanger, the construction of which is often an Al 3003 core with Al 5083 or 6061 headers, nozzles and piping.
Mechanisms of Mercury Attach
The mercury can degrade aluminium materials via three basic mechanisms:
Amalgamation
Amalgamation is the process by which mercury forms liquid solutions with various metals, primarily Al, Au, Ag and Zn. Of these, Aluminium has engineering significance. The Aluminium is generally prevented from contact with mercury by the Al2O3 protective surface oxide. While the oxide on Aluminium is not homogeneous and contains numerous defects, in general mercury lacks the ability (due to high surface tension) to diffuse through these microscopic cracks and defects to reach the underlying metal. However, this inability to penetrate the protective oxide layer may be mitigated by thermal or mechanical stresses, by abrasion and by some chemical environments.
Once mercury has breached the aluminium oxide and come in contact with the underlying metal, the rate of amalgamation depends, largely on the metallurgy and microstructural condition. It is observed, for example, that mercury amalgamates selectively with weldments and more rapidly with some alloys. Amalgamation generally results in surface etching and pitting as long as no water vapour is present. It can result in the loss of mechanical strength in weldments.
Amalgam Corrosion
Amalgam corrosion is the combined action of mercury and moisture on susceptible materials, primarily Al, Cu and Sn. The difference between the mode of attack and simple amalgamation is that the corrosion process requires water and propagates with miniscule amounts of mercury. The reaction is:-
Hg + Al Hg(Al) amalgam (1)
Hg(Al) + 6H2O Al2O3 . 3H2O + 3H2 + Hg (2)
Hg + Al Hg(Al) (3)
The amalgam corrosion process does not consume the mercury and hence is self-propagating so long as mercury is in contact with aluminium metal and water is available. If sufficient moisture and mercury are present, aluminium structural components can be penetrated fairly rapidly. The rate of attack is mass transfer limited but does not proceed as rapidly as liquid metal embrittlement (LME). The amalgam corrosion reaction proceeds more rapidly with some aluminium alloys, but all are susceptible to some extent.
The amalgam corrosion was unable to occur if the aluminium was not wetted by the mercury and the reaction required the presence of moisture. Nelson acknowledges that mercury can cause catastrophic attack of aluminium in the presence of 'free' water, however, suggests that in cryogenic heat exchangers the presence of water is extremely unusual, and has not been a factor in any reported leak occurrence.
Liquid Metal Embrittlement (LME)
Liquid metal embrittlement by mercury differs from amalgamation and amalgam corrosion in that LME produces rapid brittle fracture, affects a broader range of materials (Al, Ni-Cu, Brasses, Cu alloys, Sn alloys, and some stainless steels) and is generally much more severe than other embrittling processes such as hydrogen-embrittlement or stress-corrosion cracking. Once cracks have initiated, very rapid sub-critical cracking can occur even at low stresses. Cracking occurs preferentially along grain boundaries for the Al:Hg couple (and for many other couples), but transgranular (cleavage-like) fractures can also occur. Liquid metals are drawn into growing cracks so that the crack tip is always in contact with embrittling metal atoms. The rate-controlling process for cracking is still being debated, but the rate of flow of liquid within cracks may control the rate of cracking in some circumstances
Thin films of liquid metal are left behind the advancing crack tip and, hence, fracture surfaces are covered with a film of liquid mercury. For the Al:Hg system, 'de-wetting' can occur so that small globules of mercury are present on fracture surfaces. The presence of mercury on fracture surfaces can also result in the growth of oxide whiskers after fracture, a phenomenon peculiar to Al (and to a lesser extent Mg) alloys and described in the section on amalgam corrosion.
Breaching the Aluminium Protective Oxide
From the above discussion it is quite clear that for LME cracks to initiate there must be intimate contact between liquid and solid metals, with no intervening oxide films to prevent wetting and adsorption. Al alloys are covered by a thin, protective oxide film, and surfaces can be covered by liquid mercury indefinitely without any reaction until the oxide is damaged. Oxide films can be broken by mechanical processes e.g. by scribing or abrasion, by chemical processes, e.g. corrosion, or by plastic deformation of the aluminium resulting in slip steps at the surface.
Gordon favours the abrasion on the surface by hard particles in the gas or liquid streams. He suggests that as the gas entering cryogenic equipment usually consists of mainly methane, CO2 and hydrogen, it is oxygen-free. Hence the reducing atmosphere of the gas stream may prevent any reformation of the protective oxide layer once damaged from hard particles in the gas stream has occurred. Others suggest that the differential thermal expansion between the aluminium substrate and the alumina oxide being a factor of around 3 could cause the oxide to crack when the heat exchangers is warmed.
Whichever mechanism is operative in this situation the brittle nature of the cracking, the intergranular nature of crack propagation and delamination, and the presence of Hg on the fracture surface supports the Hg induced LME failure mechanism.
Summary
LME of aluminium alloys requires:
- Mercury in direct contact with the aluminium
- A susceptible aluminium microstructure and alloy composition
- Temperatures above the freezing point of mercury (-38°C)
- Stress (mechanical or thermal) or residual stress from welding
- Magnesium as an alloy component in the base metal or weldment
- Could be exacerbated where Al3Mg2 precipitates on grain boundaries.
The conclusion that the aluminium heat exchanger failed due to mercury induced LME is based on the following:
- The heat exchanger was manufactured from a material potentially susceptible to Hg LME
- Hg known to be present in the heat exchanger
- Brittle nature of cracking
- Hg on the fracture surfaces
- White oxide whiskers on the fracture surfaces
- Hg along the crack boundaries throughout the fractured area.
Sincere thanks go to Dr Stan Lynch (DSTO now retired) for his invaluable assistance in this investigation.
Those who would like to read more about this failure are directed to 'The interaction of mercury and aluminium in heat exchangers in a natural gas plants', R. Coade, D. Coldham, May 2006 · International Journal of Pressure Vessels and Piping.
Footnotes:
W Gordon. 'Assessing the susceptibility of an LNG Plant to Mercury-induced Attack', 14th International Corrosion Congress Proceedings, Cape Town, South Africa, Oct 1999.
M Pinnel & J Bennett, 'Voluminous Oxidation of Aluminium by Continuous Distribution in a Wetting Mercury Film', J of Mat Sci, 7, 1972, p1016
L Bruce & G Wise, "Comments on - Voluminous Oxidation of Aluminium by Continuous Distribution in a Wetting Mercury Film', J Mat Sci, 9, 1974, p335
D R Nelson, 'Mercury Attack of Brazed Aluminium Heat Exchangers in Cryogenic Gas Service', Proceeding of the 73rd GPA Annual Convention, New Orleans, March 1994, pp178-183
M.O. Speidel, p. 302, The Theory of Stress Corrosion Cracking, NATO, 1971, and
J.A.Feeney and M.J. Blackburn, p. 389, ibid
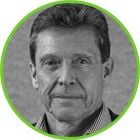)
Tags:Analytical ServicesCase StudyEnvironmentReliabilityEfficiencySustainabilityPower PlantsHeat exchange |