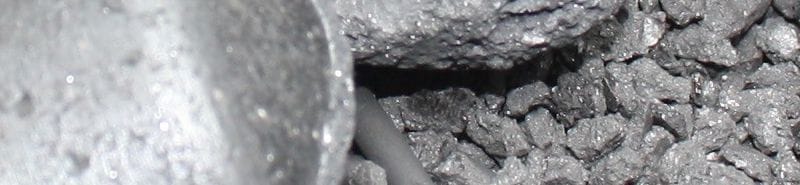
Briquetting and Agglomeration
Briquetting, Pelletisation and Agglomeration
Benefits of Agglomeration
hrl: agglomeration services assist clients in achieving a range of technical, environmental and financial benefits which can include:
- Reduced materials volumes and improved material consistency for storage, handling and transport
- Convert the material into a form that can be utilised in a downstream process
- Alleviating dust related issues including explosion, fire, self-heating, safety, and environmental risks
- Reduced volumes of waste material requiring disposal and thus reduced disposal costs
- Converting waste or low value materials into higher value products
hrl: Agglomeration Services
hrl: services related to agglomeration and pelletisation include:
- Laboratory analysis of feedstock and agglomerates
- Dangerous Goods Classification
- Technical evaluation and selection of agglomeration technologies
- Assessment of suitable binding agents
- Pilot-scale agglomeration studies
- Agglomerate quality testing including chemical properties, mechanical strength, thermal strength and behaviour, DG classification (DG 4.1, 4.2, 4.3); and assessment of emissions during combustion
- Larger scale trials to produce larger batches (tonne quantities) of agglomerates
- Detailed engineering/feasibility study for agglomeration plant, including flowsheet development, cost estimation of project viability assessment
- Sourcing/procurement of equipment and project implementation
- Engineering support including optimising existing processes
The agglomeration services are backed by hrl: analytical, thermal and mechanical testing capabilities, and supported by its team of chemical, mechanical, environmental and materials engineers and scientists.
Materials Agglomerated by hrl:
Raw materials:
- Coal, coke, char and carbons
- Minerals including iron ore, synthetic rutile, titanium dioxide and spodumene
- Lime, cement and fly ash
- Paper and cardboard
- Bark, wood and sawdust
- Agricultural by-products
- Chemicals, plastics and fertilisers
Wastes:
- Tailings and slurries
- Fine particulate material captured in dust-extraction systems
- Steel, nickel, lead and zinc oxide fines
- Steel, aluminium and a range of other milling waste
- Chemical, plastic and paper wastes
- Refuse derived fuel (RDF) and municipal solid waste (MSW)
- Chicken litter and animal manure
- Biomass and agricultural waste
hrl: Agglomeration Equipment
The range of agglomeration equipment operated by hrl: includes:
- Double-roll press briquetter for producing pillow or almond-shaped briquettes
- Pellet mill to produce 4 and 6 millimetre diameter pellets
- Drum pelletiser to produce 10 to 30 millimetre spherical pellets
- Reciprocating stamp press briquetter to produce 90 millimetre diameter briquettes
- Kneader-extruder to produce pellets from viscous pastes
- Screw extruder to produce agglomerates from 20 to 50 millimetre in various shapes
- Bench-scale stamp press
- Agglomerate quality testing apparatus
- Auxiliary equipment including mills, dryers, conveyors and mixers
Agglomerate Quality Testing
- A range of tests and activities can be performed to assess the quality of agglomerates
- Pellet mechanical durability test (I.S.CEN/TS 15210-1:2006)
- Drop shatter resistance (2 or 5m drop test)
- Abradability testing
- Compressive strength
- Agglomerate density
- Resistance to shock heating
- Visual appearance
- Moisture content
- Simulation in downstream processes
- Plant combustion and kiln trials, including plant performance and emissions testing
hrl: assists clients by employing advanced agglomeration techniques to convert valuable materials from particulate, solid and liquid waste streams into pellets, pills, balls or briquettes that can be recycled or reused.