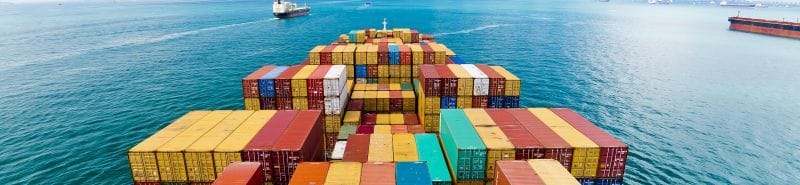
QA of Overseas Manufacture
Challenges
Limited Australian-based capacity for manufacturing high-pressure high-temperature equipment such as that required in thermal power stations and processing plants often forces the owners and operators of those plants to turn to overseas manufacturers.
A potential low-cost option especially from Asian-based suppliers overseas manufacturing comes with challenges. Such challenges can include:
- confidence in manufacturer's Quality Management System, their capabilities and capacity
- understanding of procurement requirements and design specifications to ensure compliance with Australian standards, and statutory and regulatory requirements
- plant owner/operator's presence during design, manufacturing, packaging and shipping of plant.
Solutions
HRL provides a comprehensive range of independent, specialist services that address the specific challenges Australian-based companies face when purchasing high-pressure high-temperature equipment from off-shore suppliers. The HRL team that provides the services includes professionals with comprehensive expertise in quality assurance and control, project management, mechanical engineering, metallurgy, materials and chemical engineering.
By using the experienced independent services offered by HRL companies can manage and control the quality of the plant they purchase. Control commences with verifying plant design, and continues through the procurement chain to ensure what is specified is delivered in compliance with Australian Standards and other statutory and regulatory requirements.
The comprehensive range of independent specialist services HRL provides includes:
Quality services
Supplier evaluation
Quality control
Providing independent expert inspections at each critical stage including:
- Preproduction raw materials or components, patterns/mould
- Production first products out of the manufacturing process or any of its stages
- Pre-shipment quality, where final inspection services are required
- Loading ensuring packaging/loading plans are adhered to, and the right quantity is shipped.
Expediting services
Independent monitoring and supervision to ensure contract requirements are met including specified quality and schedule. Specific services include:
- reviewing all project documentation
- providing quality assurance and other documentation required to meet quality, regulatory and statutory standards
- monitoring/scheduling work progress
- overseeing daily work to ensure specifications are met
- assessing delivery schedules
- preparing progress reports.
Benefits
By engaging HRL to support the fabrication of plant off-shore, clients enjoy peace of mind. They know the equipment they receive will represent cost-effective procurement, at the required quality, and be delivered on schedule.
HRL's engineers support clients through their involvement in verifying plant design, identifying local materials that meet Australian specifications, determining inspections and test requirements, verifying materials and non-destructive testing, factory acceptance testing and progress reporting.