Food Organisation Case Study
HRL works with leading food organisation to mitigate autoclave cracking and improve production performance
Challenge
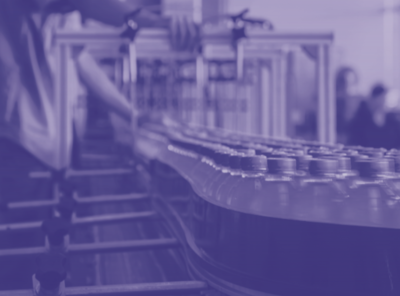
Solution
HRL was engaged to gather data and determine why these failures were occurring. Carrying a large stock of various transducers to measure strain, temperature, force, displacement, vibration, and much more, HRL was able to install strain gauges and thermocouples to the autoclave to understand what was happening during its operation. The data obtained determined that high stresses occurred due to severe temperature differences, resulting in thermal fatigue cracking.
HRL used this data in conjunction with plant system data to change the design and operation of the autoclave, and ultimately increase the fatigue life of the autoclave and therefore its availability.
HRL also performed engineering assessments of the autoclave using the data obtained from testing to determine the critical crack size and failure mechanism. Should further cracking occur, this means the autoclave can remain in service if cracks are within the critical sizes. Repairs can then be scheduled with less impact on production.
Results
To test is to know, and by engaging HRL this food organisation gained the data needed to identify the cause of the problem. Using the test data, they were then able to make informed decisions about operational and design changes to mitigate further cracking and increase the availability of the autoclave. This resulted in less lost production and increased savings.
Testing differentiates HRL from other providers in that HRL obtains actual data from equipment operation. HRL then uses the data to determine actual boundary conditions for modelling and assessments, unlike other organisations which often assume boundary conditions that are incorrect and therefore fail to determine the real cause of the problem.
Throughout the project, HRL's stress analysts worked closely with the client to understand the operational product process of the autoclave. HRL also helped the client to understand the stress and life impact that occurs due to thermal restraints within the autoclave. The autoclave remains in service today, performing its required production process. The client was very pleased with the outcome and has enjoyed the commercial benefits of enhanced equipment availability.