A large Australian operator of wind turbines experienced a near catastrophic failure, with rogue weld repairs causing severe cracking in a major forging. These untraceable weld repairs cast doubts over the safety of an entire fleet of recently-installed turbines. Wind turbines are constructed of many components sourced through international supply chains that can't always be verified as quality suppliers. The unknown origins of imported components pose a real risk to Australian wind turbine owners and operators.
Wind Tower Shaft Case Study
HRL resolves potential catastrophic failure of wind turbine components
Challenge
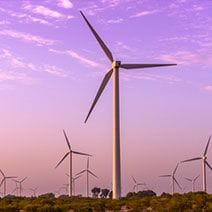
Solution
HRL was engaged to develop an in-situ inspection method to rapidly determine the presence of rogue weld repairs. Leveraging its inspection experience and expertise, HRL first validated the technique on sample components before implementing on site. Exploiting a phenomena related to electromagnetic testing technology that allowed a very fast inspection of the potentially unsafe components, HRL confirmed the presence of rogue weld repairs in the component identified. HRL also concluded that some effort had been made by the manufacturer to hide the rogue weld repair from the client. Further site inspections of the other wind turbines proved that this was an isolated case with no further occurrences.
Results
HRL responded quickly to meet the client's urgency in addressing these major safety concerns. The site inspections conducted quickly put the client's anxiety at ease, as it was proven that the rogue weld was an isolated case with no other occurrence on this wind farm.